原创论文︱大直径穿湖顶管回退施工关键技术研究 原创 杨睿,等 中国给水排水 2024年10月10日 14:14 天津 点击蓝字 关注我们 摘要:顶管技术具有施工方便、不中断地上交通、无
核心提示:原创论文︱大直径穿湖顶管回退施工关键技术研究
原创 杨睿,等 中国给水排水
2024年10月10日 14:14 天津
点击蓝字
关注我们
摘要:顶管技术具有施工方便、不中断地上交通、无噪声、无环境污染等优点,因此广泛应用于地下空间的开发利用,但在实际的顶管顶进施工中难免遭遇无法清除的障碍物,造成无法继续顶进的问题。依托武汉汤逊湖污水处理厂尾水排江顶管工程,提出一种施工方便、高效率的大直径顶管退管方法,阐述了退管工艺流程,并总结了施工过程中的关键技术,同时就二次顶进设
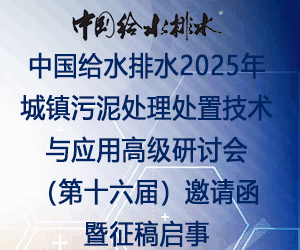
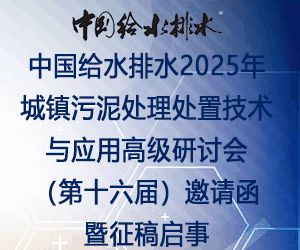
摘要:顶管技术具有施工方便、不中断地上交通、无噪声、无环境污染等优点,因此广泛应用于地下空间的开发利用,但在实际的顶管顶进施工中难免遭遇无法清除的障碍物,造成无法继续顶进的问题。依托武汉汤逊湖污水处理厂尾水排江顶管工程,提出一种施工方便、高效率的大直径顶管退管方法,阐述了退管工艺流程,并总结了施工过程中的关键技术,同时就二次顶进设计准备进行设定。实际工程效果表明,该退管方法适用于大直径顶管退管工程,能够很好地解决大直径顶管退管回退阻力大、反推力不足的问题,从而有效提高退管施工效率,降低施工成本。
杨睿,硕士,工程师,主要从事桩基础、地下结构预制装配化等设计及施工方面的工作。
随着城市化的不断发展,地下空间的开发与利用不断受到重视。顶管作为一种不需要进行开挖的技术,具有效率高、施工不影响周边环境等优势,越来越被广泛应用于市政工程中。但顶管工程施工难免遇到复杂的地质环境、碰到无法清除的障碍物,此时就需要采取管道回退的方案。目前针对管道回退,马敬豹等提出了钢绞线在长距离故障顶管回退中的应用优势,并成功应用于上海市白龙港片区污水输送干线大口径长距离过江顶管工程,成功拔出95 m故障顶管。屈勇等总结了当前顶管障碍物处理的相关技术,针对顶管回退提出了套管技术。巨宏伟通过对重庆市观景口水利枢纽引水隧洞硬岩顶管回退技术的研究,总结了长距离硬岩顶管回退技术的技术要点。甄亮通过数值模拟的方法分析研究了顶管在退管过程中对周边环境的影响,并提出了控制地表变形的方法。目前相关研究大多针对小直径顶管回退技术,缺少对大直径顶管回退方法的研究。针对武汉汤逊湖顶管工程穿湖段4#~3#遇障无法继续顶进的问题,优化创新反顶油缸反拉钢架的退管方法以及边退边填的工艺流程,对大直径顶管退管的原理、工艺流程、关键技术以及防护措施进行阐述。
汤逊湖污水处理厂尾水排江工程项目4#~3#穿湖段隧道全长1492.65m,顶管机自4#竖井出洞始发至3#竖井进洞接收,平面线形为直线;4#竖井管中高程3.2m,3#竖井管中高程4.7m,竖直线形为0.1%上坡。顶管套管为钢筋混凝土预制管道,管道内径4m,外径4.8m,管节衬砌厚度为400mm,每节管道长度为2.5m,管节之间采用高刚性承插口进行连接。4#竖井采用沉井施工工艺,沉井内径13m,壁厚1.2m,地面标高20.8m,洞门中心标高3.2m。根据前期地勘资料及沉井施工期间的地层揭示情况,顶管施工穿越地层段以粉质黏土、黏土等全断面土层为主,在4#竖井出洞108 m范围内底部存在局部砾卵石。针对此类地质条件,4#井顶管机选用普通泥水平衡顶管机,刀盘超挖外径D4850mm,刀盘采用中心鱼尾刀+保径贝壳刀+先行撕裂刀+正刮刀组合,正反旋转出渣。为了应对淤泥质黏土采用双排出渣口设计,刀盘进渣口采用锥形设计,有利于渣土顺畅地流入土舱,避免渣土堆积,刀盘背部配置有搅拌棒,可对渣土进行搅拌,增强渣土的流动性,减小刀盘切削扭矩,减少渣土聚集黏结的可能性,降低刀盘本体磨损。考虑到地层底部的砾卵石(粒径为20~80mm),设计刀盘开口尺寸最大100mm,保证砾卵石可以正常进舱排出。顶管及刀盘结构如图1所示。
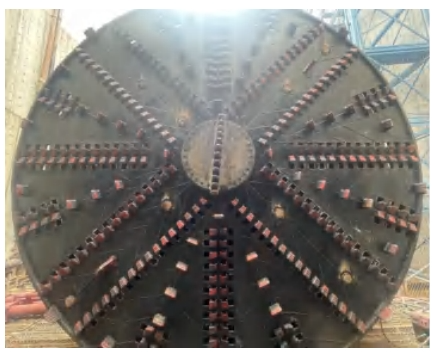
图1 顶管机刀盘结构
该段顶管严格按照顶管专项施工方案要求开始顶管施工并顺利出洞始发,在顶进20.1m时(第8节管节顶进施工中),主顶千斤顶的顶力升至1000t(106 N),顶进困难,现场立即停止顶进。通过钻芯检查,在顶管机刀盘顶进过程中发现尺寸约300mm钢筋混凝土块和尺寸超过200mm的卵石块(见图2),由于顶管机设备在前期选型过程中未充分考虑遇大直径钢筋混凝土块、孤石处理措施,因此需将已顶进管节和设备全部从洞内退出,通过对顶管机进行改造或更换,增加二次破碎舱和刀盘开口率等方法,使其满足二次复顶的要求。
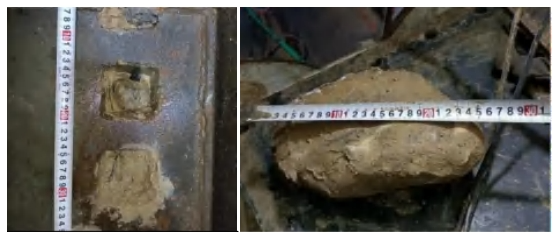
图2 遇障实物
大直径顶管退管主要按照“逐段松管、整体退管”的思路进行施工,采用螺纹钢组作为退管拉索,一端与隧道内顶管机机头连接,另一端与沉井内反力架连接,同时在洞口两侧设置千斤顶作为反推装置,带动管道及顶管机整体回退。退管的同时,向机头前方空洞内泵送混合回填料填充,防止地面沉降或开裂。拔出顶管机头后更换具有大开口率、带二次破碎功能的复合型顶管机,重新规划顶进路线,采用原始发井、接收井作为进、出工作井进行复顶。具体包括:顶管机内设备拆除→施工装置安装(反顶后背墙、反力架、螺纹钢组、千斤顶)→逐段松管→整体退管(退管过程中采用注土系统同步泵入回填料)→钢板桩封堵(机头留在孔洞1.2m)→地基加固→钢板桩拔出、机头退出→复顶。
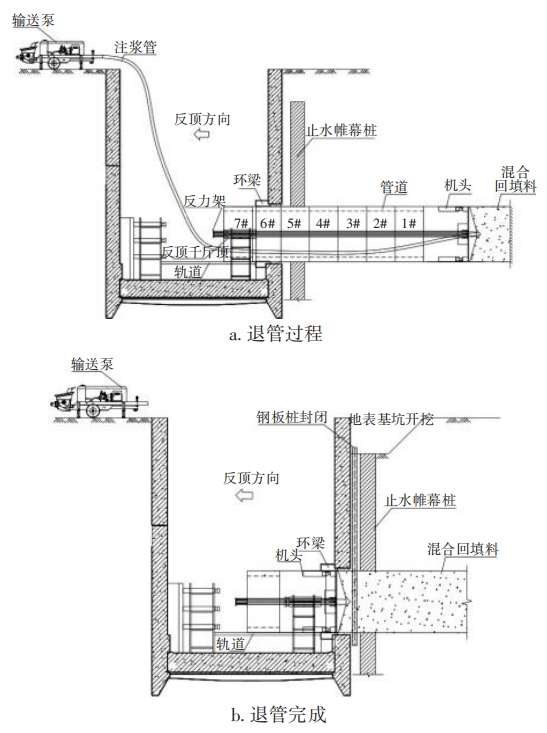
图3 退管施工工艺流程
由于沉井内壁为弧形结构,为保证后背墙整体受力均匀,退管施工前需在洞口管道两侧设置反推后背墙。后背墙整体呈扇形结构,最厚处为40cm,宽0.69m,高5m,采用C30混凝土结构。同时为保证后背墙整体受力的稳定性,在后背墙内部设置单层双向钢筋网片,钢筋网片采用Ø10mm钢筋加工,后背墙主要受力区(上部1.7m范围内)钢筋网间距为8cm×8cm,下层非受力区域钢筋网间距按8cm×20cm设置。通过计算退管时所需反顶力进行选型,沿管道轴线左右对称布置,每侧布置2台千斤顶,退管过程中4台千斤顶应共同作用,规格一致,行程同步,每台千斤顶的使用压力不大于额定压力,油路必须并联,每台千斤顶均备有独立的控制阀。另外,为保证后背墙整体受力,在千斤顶和后背墙之间需设置一层钢垫层,垫层采用3cm厚钢板,宽0.7m,高2m。钢板与后背墙内预埋钢筋焊接固定,形成整体,为顶管的反力提供一个垂直的受力面整体,保证受力更均匀。反力架采用双拼H900mm×400mm×20mm×26mm型钢,型钢采用Q235材质,反力架全长8m,在与螺纹钢连接处需提前在翼缘板上开设4个DN45孔洞,用于安装螺纹钢,并采用缀板补强;反顶千斤顶与反力架接触面同样采用钢板补强,确保其受力均匀。反力架在管节开始退管前再进行安装,先用门机反力架吊装至设计高度(管道中轴线位置),人工将螺纹钢从反力架上预留锚孔内穿过,端头采用螺栓锚固。顶管机头牛腿支架与反力架采用螺纹钢组连接,如图4所示。螺纹钢组采用Ø40mm的PSB830型精轧螺纹钢,其抗拉强度为1 030 MPa,每根螺纹钢极限拉力为90t(9×104N)。螺纹钢布设在管道左右两侧,单侧螺纹钢组由4根组成,两侧共计8根,可以提供720t(7.2×105N)的拉力,满足退管拉力要求。
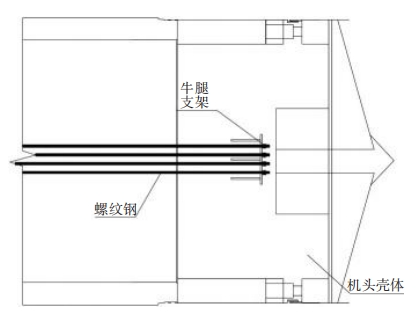
图4 螺纹钢与机头连接
大直径顶管整体退管时摩擦阻力较大,因此必须采用润滑技术进行减阻:一方面减小反推力,保证退管效率,另一方面降低管节磨损,以便复顶二次利用。退管时主要采取的措施:通过管道上注浆孔向管道外同步注浆,形成泥浆套,降低管道摩擦阻力;在洞口防水橡胶圈上涂润滑油,防止管道回退破坏橡胶结构,影响再次顶进时的密封效果。正式退管前需进行试拉,逐步增加反顶力,顶力增量按总设计顶力的20%进行控制,当压力提升至设计压力但管道仍未拖动时,立即停止退管,查明原因,采取相应措施。正式退管时,根据试拉确定的反拉力控制反顶千斤顶,顶推反力架,将管道及顶管机整体回拉。施工时,应控制好退管速率,每次退管长度不得超过30cm,退管速度控制在0.5m/h以内。退管过程中可能引起周边土体坍塌,从而导致地面沉降等情况。为保证施工安全,整体退管时,同步向机头前方空洞内注回填料填充,保证地层的稳定性。针对回填料泵入性、泌水率、抗压强度等性质,采取正交试验的方法选择最优配方。通过实验室性能测验确定最优回填料具体配置:粉煤灰∶水泥∶黄黏土∶水=150∶7.5∶17∶80。回填料性能参数:初凝时间控制在5 h,终凝时间控制在12h以内,泌水率3%,28d强度为0.5~1.0MPa。回填料的实验室状态见图5。采用混凝土车载输送泵作为泵送设备,设备布置在沉井地面操作室旁,为减少管道安拆,直接采用顶管机的排泥管作为泵管,在刀盘面上方开设注浆孔,与泵管连接。将泵管与地泵连接牢固,检查无误后进行回填料泵送施工。管道回拉的同时,边退管、边注回填料,注浆压力控制在0.2MPa左右,根据现场实际施工情况进行调整。在填充过程中应保持压力稳定,如果发现压力过小,先停止退管,继续注入回填料,直至压力上升至设计值,再开始退管。注浆时,采用注浆量及注浆压力双重控制;以注浆量控制为主、压力控制为辅。严格控制回填料注入量,根据计算退空区域体积量,每退管1m,至少向掘进机前方由掘进机退出的空间中注入20m3回填料,要求全部由回填料填充,保证回填密实。另外,退管回拉的速度不可过快,退管速度与注浆压力、速率及混合料的初凝时间等相匹配。根据同类型项目退管施工经验,每天回退一节管道后,停滞5h,待回填料达到初凝后,方可继续回退后面管节。
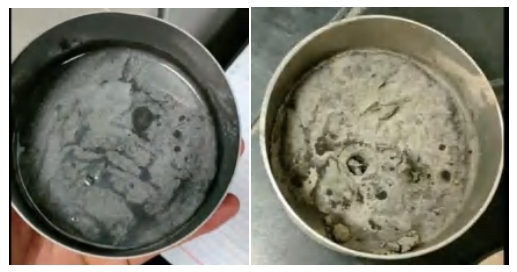
图5 回填料的实验室状态
在管道回退过程中,回填料不及时、注浆压力不足等容易引起前方土体塌陷,因此施工中加强沉降监测是工作的重点。监测要及时准确,根据监测数据对退管参数进行调整,做到信息化施工。退管施工前全面检查输送泵及输送管道等设备,确保管道退管过程中设备能正常工作。控制好回退速度,在地面沉降较大时,回退速度控制在25~50cm/d,并根据每天测量参数不断调整回退速度及退管参数。
大直径顶管直接退管时所需拉力较大,因此为了降低退管难度,采用小型千斤顶对管道进行逐段顶管,将管道松开,降低摩擦阻力系数后,再整体退管。4#竖井共顶进7节管道,其中2#、4#及6#管道上设有纠偏油缸仓(见图6),在纠偏油缸仓埋设小型千斤顶,提供松管的反顶力。松管时,每组管道内4个小型千斤顶同时顶推,将前方管道向沉井方向顶进,使管道分节段松开,最后机头部分直接采用反顶千斤顶及反力架配合,在螺纹钢牵引下,带动机头部分移动。在回退每一节管道之前,均需按照上述方法进行分段松管,以减小整体退管的摩阻力。
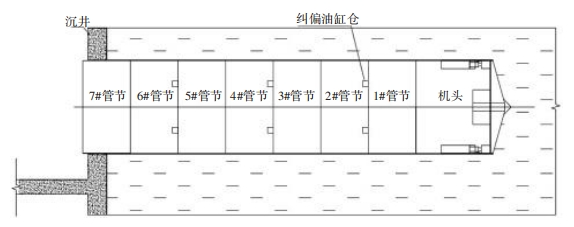
图6 管道纠偏油缸仓位置
在退管过程中,为防止最后机头拉出过程中洞口坍塌,在机头未全部退至工作井内时(机头最后约1.2m仍留在洞口内),暂停退管,做好阻退措施,同时对洞口进行封闭。现场主要采用两种阻退措施,一方面利用主顶千斤顶及阻退支架作为阻退手段,另一方面由于在吊管过程中,主顶千斤顶无法有效起到防退效果,因此采用管道两侧的三角反力架作为止退装置。洞口封闭采用钢板桩进行围护封闭,前期顶管施工时,在井壁外侧0.75m处施作一圈素混凝土桩作为止水帷幕桩,为方便钢板桩施工,钢板桩设置在素混凝土桩外侧,距离井壁外侧约2.3m。钢板桩采用拉森SP-Ⅳ型钢板。钢板桩施作宽度为6m,两侧与井壁合围封闭。为保证封闭效果良好,钢板桩的桩底应插入管底以下1m以上。为了防止机头退出后洞口处水土流失,造成地面塌陷沉降的情况,必须先对洞口上部的土体进行加固(机头最后约1.2m仍留在洞口内),待加固完成且加固体强度达到要求后,再将顶管机拉出洞口,工程中采用钻孔压密注浆的方法将上部土体连成一个整体。首先根据顶管顶进轴线按梅花状布设钻孔(见图7),设置4排钻孔,排距1m,孔距1m,成孔孔径100mm,孔深13m;然后埋设Ø89mm袖阀管,注浆体设计直径为500mm;当最外排的孔成孔后即进行孔口清理,同时开始分区域、分时、分段注浆,浆液用配比为水∶水泥∶水玻璃=417∶417∶600 的双浆液,注浆压力一般控制在0.2~0.5MPa,当注浆压力达到终压时需要维持10min以上以确保浆液在土体中的渗透。最后进行提管,每个注浆孔每段上提70cm,同时在提管过程中注意用力均匀,按一定步距,及时快速地逐段灌注浆液。工程中一般采用双塞系统止浆塞分段注浆。
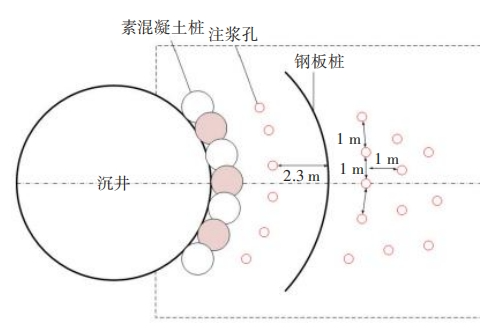
图7 压密注浆孔排布位置
对汤逊湖大直径穿湖顶管工程遇障无法顶进的问题进行了分析研究,并从实际工程情况出发,提出了反力架反顶油缸拉管法,对退管装置的安装、减阻润滑、反拉退管以及“边退边注”的注土系统进行了介绍,同时对大直径顶管退管中分段松管、洞口封堵及阻退、洞门加固等关键技术进行了总结。相关施工工艺及方法在现场成功实施,整个退管过程进展顺利,包括顶管机在内的超过20m退管施工仅耗时1周,机头前方地面沉降始终控制在3cm以内,全程未出现地面塌陷的情况;退出管节的结构及外观保存完好,后续被全部用于二次顶进。该大直径顶管遇障退管解决思路,可为今后类似地层顶管施工提供技术支持。
本文的完整版刊登在《中国给水排水》2024年第6期,作者及单位如下:杨睿1,2,3,曾德星1,2,3,崔旭辉1,2,3(1.中交第二航务工程局有限公司,湖北 武汉 430040;2.长大桥梁建设施工技术交通行业重点实验室,湖北 武汉 430040;3.交通运输行业交通基础设施智能制造技术研发中心,湖北 武汉 430040)
杨睿,曾德星,崔旭辉.大直径穿湖顶管回退施工关键技术研究[J].中国给水排水,2024,40(6):126-131.
YANG Rui,ZENG Dexing,CUI Xuhui.Research on key techniques for backward construction of large diameter pipe jacking under a lake[J].China Water & Wastewater,2024,40(6):126-131(in Chinese).
制作:文 凯
审核:李德强
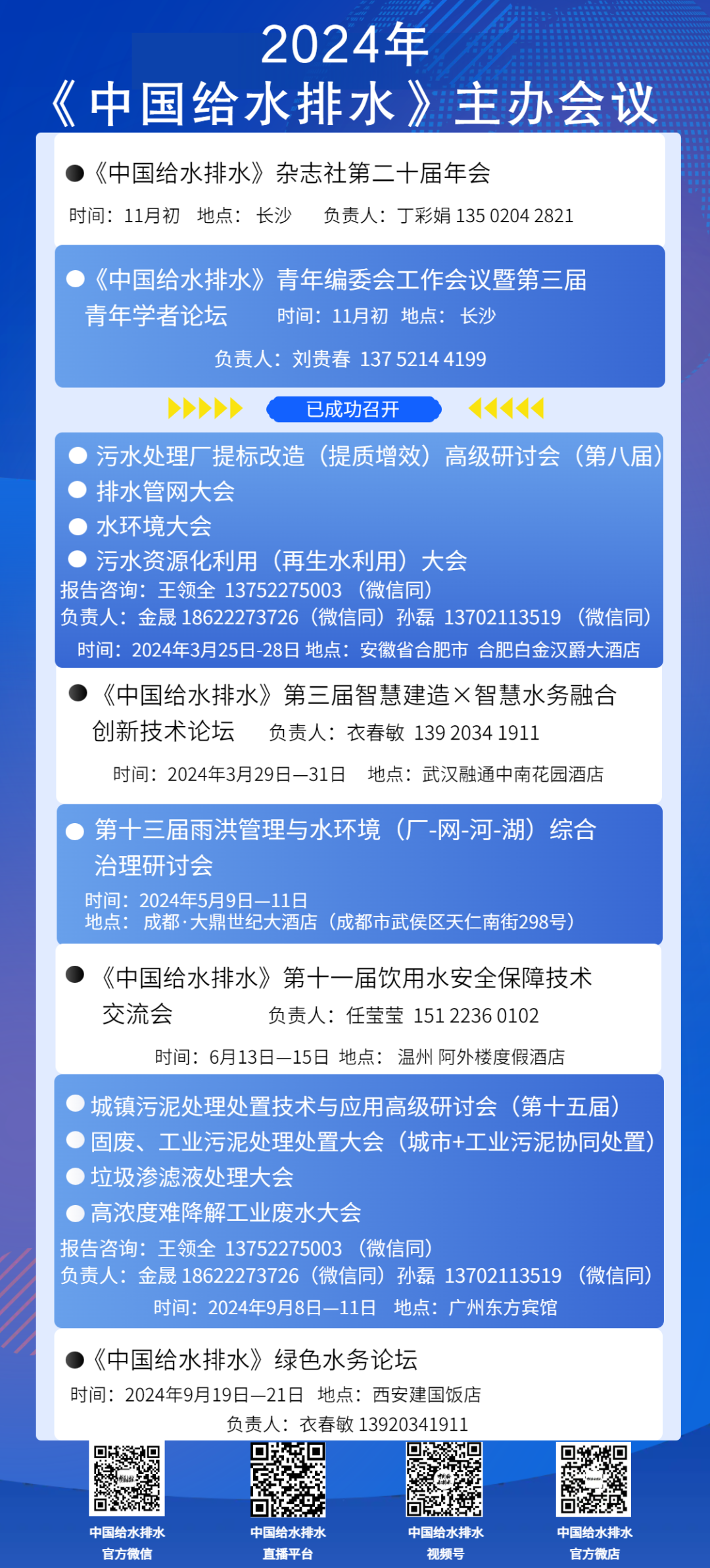
投稿咨询:022-27835707
广告咨询:022-27835639
发行咨询:022-27835520
官方网站:www.cnww1985.com
联系邮箱:cnwater@vip.163.com
[ 行业资讯搜索 ]
[ ]
[ 打印本文 ]
[ 关闭窗口 ]